According to their makers, the solar panels have an energy conversion efficiency of 10.8% and “sufficient” tensile strength and impact resistance. The research group said it used natural fiber composites as environmentally friendly alternatives to conventional polyethylene terephthalate (PET) backing sheets.
An international research team has developed a solar panel that uses a backsheet made from a natural zeolite polyester resin as an alternative to conventional polyethylene terephthalate (PET) backsheets.
According to the makers, the proposed innovation is intended to reduce the environmental impact of PET backsheets and improve the thermal and mechanical properties of the solar module. The natural fiber outer layer was produced via vacuum-assisted resin transfer molding (VARTM), which the scientists say ensures optimal thermal management and insulation.
In the newspaper “Extensive research on zeolite polyester composite coated sheets for environmentally friendly solar panels for improved panel performance and reduced panel temperature”, published in scientific reportsthe research group explained that using a natural fiber coated with zeolite polyester resin was key to improving performance and reducing heat accumulation in the panels.
“The use of zeolite-polyester composites with natural fibers provides excellent structural integrity, uniformity and reliability,” the scientists emphasized. “Although the initial costs may be higher, the long-term benefits include lower maintenance costs and better performance, especially under harsh conditions.”
The VARTM process uses a vacuum to facilitate resin flow into a fiber array contained within a molding tool covered by a vacuum bag. After impregnation has taken place, the composite part can be “cured” at room temperature, whereby a post-treatment can be carried out if necessary.
The researchers started the process by waxing the surface of the production table, marking the dimensions, installing spiral tubes and applying sealing tape. They then used the film to create a “smooth” finish for the back sheet and placed other fiber mats on top of the film. Then another layer consisting of peel-ply and a green mesh was placed on top, followed by connecting the vacuum tube to the coil tube with a T-connector.
Furthermore, an input port for single-layer fibers was placed in the center and two more input ports were deployed diagonally. They then placed a vacuum cover on the perimeter of the sealing tape. “The size of the backsheet was 20 x 20 cm, and the thickness of the sheet remained 1.5-3 mm,” the researchers said. “For each layer of fiber supplied, 90 g of zeolite and 135 g of polyester were used.”
The group built a 4.5W polycrystalline solar panel using Ecolam Max 3, an automatic solar panel laminator with a charging and discharging belt.
The 20cm x 20cm panel uses an aluminum frame and cells arranged in two columns, with each column connected to the bypass diode to form an independent array of cells.
According to the research team, the coated version showed an 8% increase in voltage and a 6% increase in amperage compared to conventional panels, while pure sisal panels showed a 4% higher voltage and 3% higher current.
“Coated pure sisal panels showed a 12% increase in power, while uncoated pure sisal panels showed a 7% increase compared to conventional panels,” it further explained. “The efficiency of solar panels improved from 9.75% to 10.8% with coated pure sisal and 10.2% with pure sisal fiber backsheets.”
The academics also found that the production of the sisal fibers emitted approximately 60% less CO2 and required 50% less energy than PET backsheets. “Solar panels with sisal fiber sheets exhibit sufficient tensile strength and impact resistance and reduce the operating temperature by 2 to 3 degrees Celsius, ensuring stable operation and minimizing heat loss,” they add.
Looking ahead, the group says sisal fiber-based backing sheets can be “effectively” used in solar panel production to improve performance and durability. “Implementing natural fiber-reinforced zeolite-polyester composites in solar panels not only addresses environmental concerns, but also provides a path to developing high-performance, long-lasting and sustainable solar energy solutions,” the report concluded.
This content is copyrighted and may not be reused. If you would like to collaborate with us and reuse some of our content, please contact: editors@pv-magazine.com.
Popular content
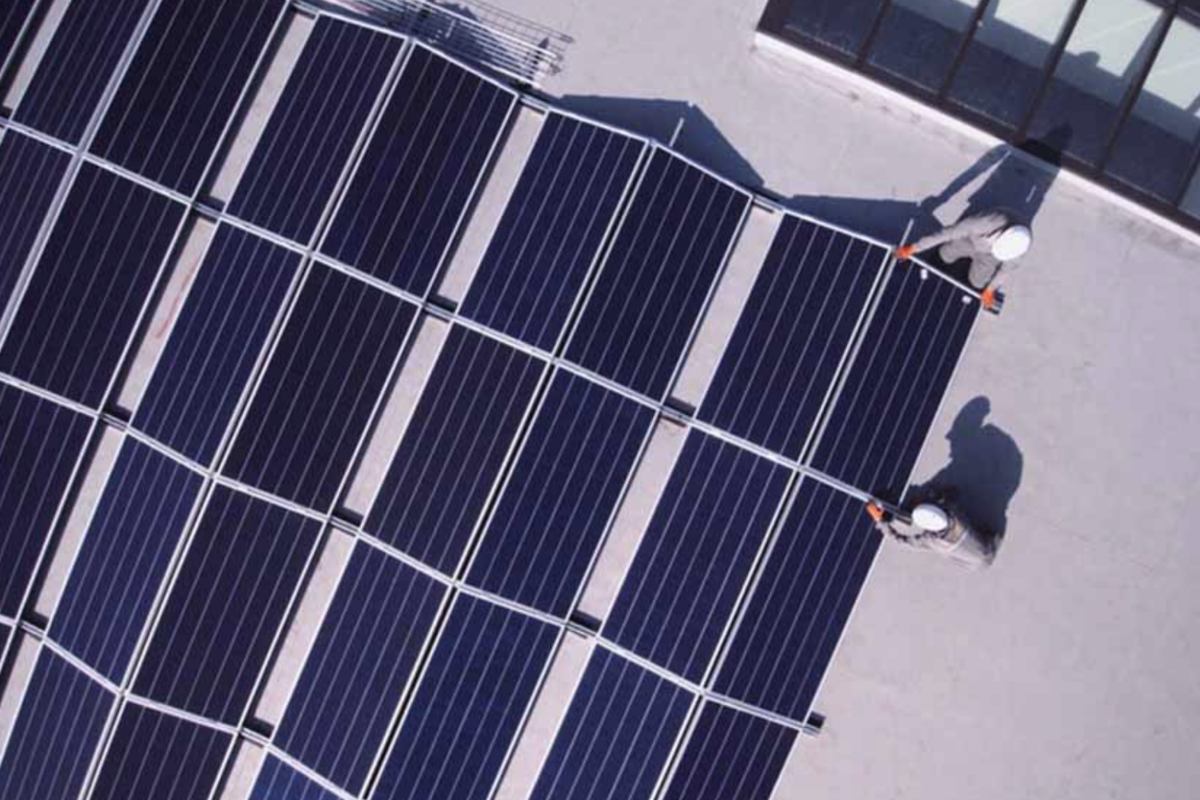