Researchers in Denmark built a prototype of a magnetocaloric heat pump for heating purposes in residential buildings. Although more work is needed to bring the system closer to commercial maturity, it can reportedly achieve a 36.9% heating power improvement with measurement feedback control.
Scientists from the Technical University of Denmark have built a prototype of a magnetocaloric heat pump (MCHP), intended for use in residential buildings.
“We are still working on system optimization and cost reduction, which can promote real-world application,” said the study’s corresponding author Jierong Liang. pv magazine. “The system is mainly responsible for this heating at a relatively low temperature and can work well with PV, which is responsible for a higher temperature level.”
MCHPs use the magnetocaloric effect to perform heating and cooling. This effect consists of cooling or heating magnetic materials with the variation of an externally applied magnetic field. It is often used to develop highly energy-efficient cooling or heating systems that require no harmful refrigerants at all.
In MCHPs the temperature changes due to a variation of the magnetic field, using these caloric effects to transfer thermal energy and produce heating or cooling power. All of these systems are based on an active magnetic regenerator (AMR) concept, where a heat transfer fluid is actively pumped through a bed of magnetocaloric material to transfer thermal energy to heat exchangers on the hot and cold sides.
The group built a full-scale MCHP prototype with 13 parallel AMR beds filled with 4.4 kg of pure gadolinium (Gd) particles as magnetocaloric material (MCM). The system uses a computer-controlled solenoid valve system to manage both flow imbalances between the AMR and flow imbalances within the AMR in real time. It also features a rotating two-pole permanent magnet with a maximum flux density of 1.46 Tesla.
“The MCMs act both as a heat exchanger for heat storage and are heated and cooled by the increasing and decreasing magnetic field, respectively,” the scientists said. “As the MCM is magnetized, heat transfer fluid is pumped through the AMR bed in the cold-to-hot direction, transferring heat from the MCM to the heat transfer fluid, and vice versa during demagnetization.”
They also explained that control of the volume of fluid displaced for each AMR and each stroke is achieved by tuning the local blowing fraction by adjusting the opening timing of each solenoid valve, without the need for additional components. “Several measurement and feedback control strategies, including AMR cold outlet temperature, AMR hot outlet temperature, and both as control feedback parameters, are explored to understand the trade-off between multi-bed controllability and device economics,” she added.
The system also uses a fluid flow system based on solenoid valves, a pump, check valves and manifolds, allowing continuous circulation of the heat transfer fluid while facilitating reciprocating flow in each AMR bed.
The MCHP multi-bed prototype, called MagQueen, is designed to meet the heating needs of an energy-efficient single-family home in Denmark. Two control strategies, namely measurement feedback control and model predictive control, were used to optimize performance.
“Model predictive control provides a solution to accelerate control convergence by providing an initial estimate of valve setting for all valves in one step,” the group points out. “Integrating model predictive control frameworks with machine learning algorithms can help identify potential system faults, such as component aging, in advance.”
The analysis showed that during the modeling, uneven flow resistance, porosity and magnetocaloric effect had a negative influence on the efficiency of the heat pump. However, with the help of measurement feedback control, the heating capacity could be improved by 36.9%.
“Model Predictive Control achieves positive results for large outliers, demonstrating the potential for faster control convergence, while addressing overshoots for small outliers requires further refinement,” the team further explained. “The convergence speed of the control is estimated to be seven times faster than the measurement feedback control strategy.”
The researchers also found that model predictive control improves heating capacity by up to 30.9% and coefficient of performance (COP) by up to 10.7%. By absorbing uneven magnetocaloric effects, it also improved COP by about 3.5%.
“Despite advances in magnetocaloric heat pumps, challenges remain, especially in adapting control strategies to multilayer regenerators with varying Curie temperatures and magnetocaloric effects,” they said, hinting at the future direction of their work.
Their findings are available in the study “Scaling up the magnetocaloric heat pump for decarbonisation initiatives”, published in Energy. “The prototype costs had not yet been estimated because some components are too large. As mentioned earlier, we continue to work on cost reduction and hopefully we can make this affordable in the future. We don’t have a plan for a field test so far due to the budget problem,” concluded Liang.
This content is copyrighted and may not be reused. If you would like to collaborate with us and reuse some of our content, please contact: editors@pv-magazine.com.
Popular content
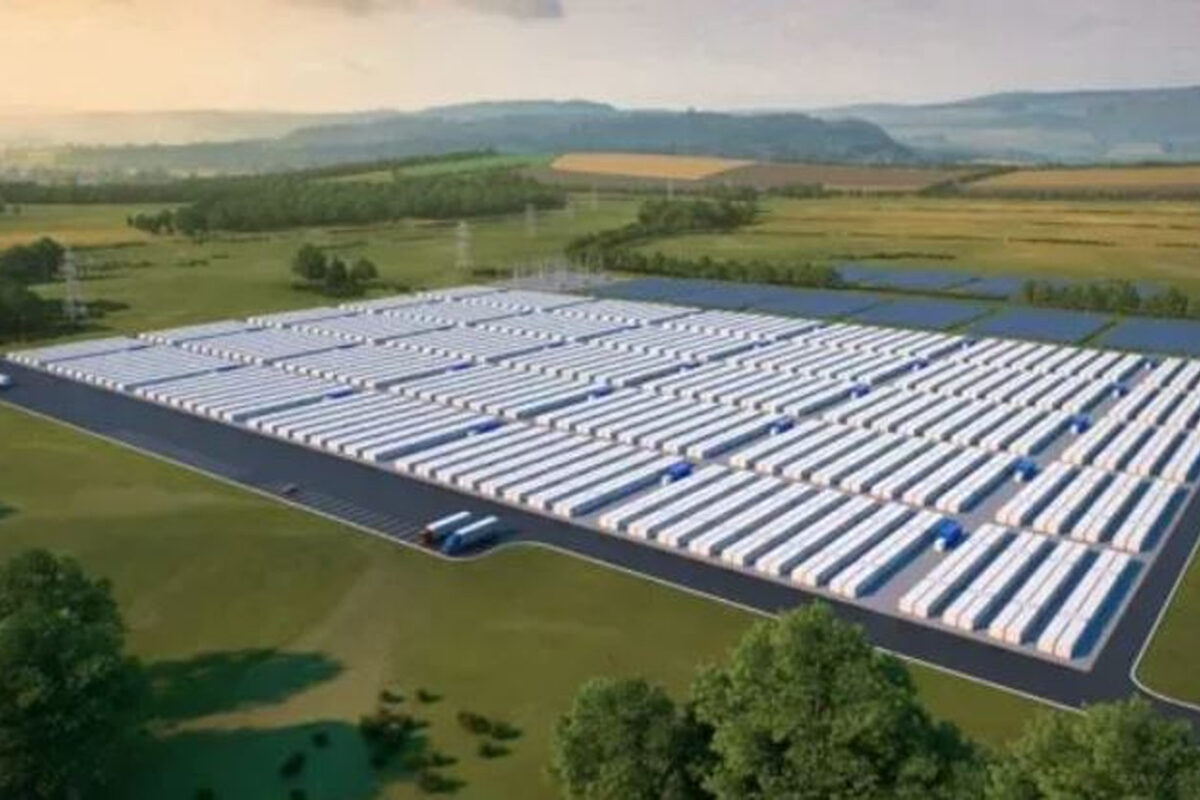