Scientists in Turkey have tried for the first time to use electrospray cooling to reduce the operating temperature of photovoltaics. They said their experiments offer promising results for the potential application of this technique in real PV systems.
Scientists from Artvin Çoruh University in Turkey have developed a new cooling technology for solar modules that uses eElectrospray cooling at research level for the first time.
This technology is used for heat dissipation in electronic components and is said to have powerful cooling capacity, small liquid supply and precise temperature control. Another important advantage is that the spray particles are smaller than with mechanical atomizers, making the droplet production more homogeneous. Furthermore, it is claimed to be easier to use and has lower energy consumption compared to conventional spray cooling.
“Electrospray cooling is a new topic in the literature, mainly used for cooling electromechanical systems of processors,” says the lead author of the study. Abdüssamed Kabakuş, narrated pv magazine. “Before this study, it has never been investigated for cooling PV systems. When the literature is reviewed, the most important characteristic of electrospray cooling is that it can achieve high heat transfer at low coolant flow rates and consumes less energy than mechanical spray systems.”
The research group wore performed a series of experiments on a small panel. “As a result of the experiments conducted on this panel, highly effective cooling performance has been obtained,” Kabakuş added. “However, this method has some disadvantages. Because the projection area of the spray ejected from a single nozzle is small, it will not be possible to use it with a single spray on industrial panels.”
Electrospray cooling combines spray cooling and electrostatic high voltage technology. It produces an electrical voltage between a metal or metal-clad surface at a high temperature and a stainless steel nozzle. The nozzle delivers a liquid with a low surface tension and the liquid particles hitting the hot surface cause cooling by removing heat due to the high heat transfer on the surface.
Image: Artvin Çoruh University, Case Studies in Thermal Engineering, Common License CC BY 4.0
The system used in the experiments uses water as a coolant. An infusion pump was used to deliver coolant to the stainless steel nozzle at a constant flow rate. The back of the solar panel was covered with a 0.016 mm aluminum foil, coated with a thermal conductive paste. To assess the module performance, the solar panel analyzer PCE-PVA 100 was used. T-type thermocouples were used to measure the operating temperature.
“The experiments were carried out for 800, 1000 and 1200 W/m2 radiation intensity, 20 kV electrical voltage and 40-60-80-100-120 ml/h coolant flow rates,” the researchers explained. “They were carried out in a laboratory environment, where the temperature of the cooling water is approximately constant and stable compared to the ambient temperature.”
The analysis showed that the panel temperature decreased as the flow rate increased, for all irradiation levels. “At flow rates above 80 ml/hour there was no significant change in temperature change. A flow rate of 80 ml/hour was determined as the optimal flow rate,” the group pointed out. “At a flow rate of 80 ml/h, the rate of temperature decrease was determined as 0.13, 0.14 and 0.15 C/s for 800-1000-1200 W/m2 of the radiation treatments.”
The measurements also showed that the efficiency of the solar panels increased by between 24.2% and 56.5%,
The cooling technology was presented in the study “A new approach to cooling photovoltaic panels: Electrospray cooling”, published in Case studies in thermal engineering. “In future studies, a multi-nozzle electrospray system will be established for cooling industrial panels and the cooling performance will be investigated,” Kabakus said. “Only after the usability for industrial panels has been proven will a calculation of the system costs be made.”
This content is copyrighted and may not be reused. If you would like to collaborate with us and reuse some of our content, please contact: editors@pv-magazine.com.
Popular content
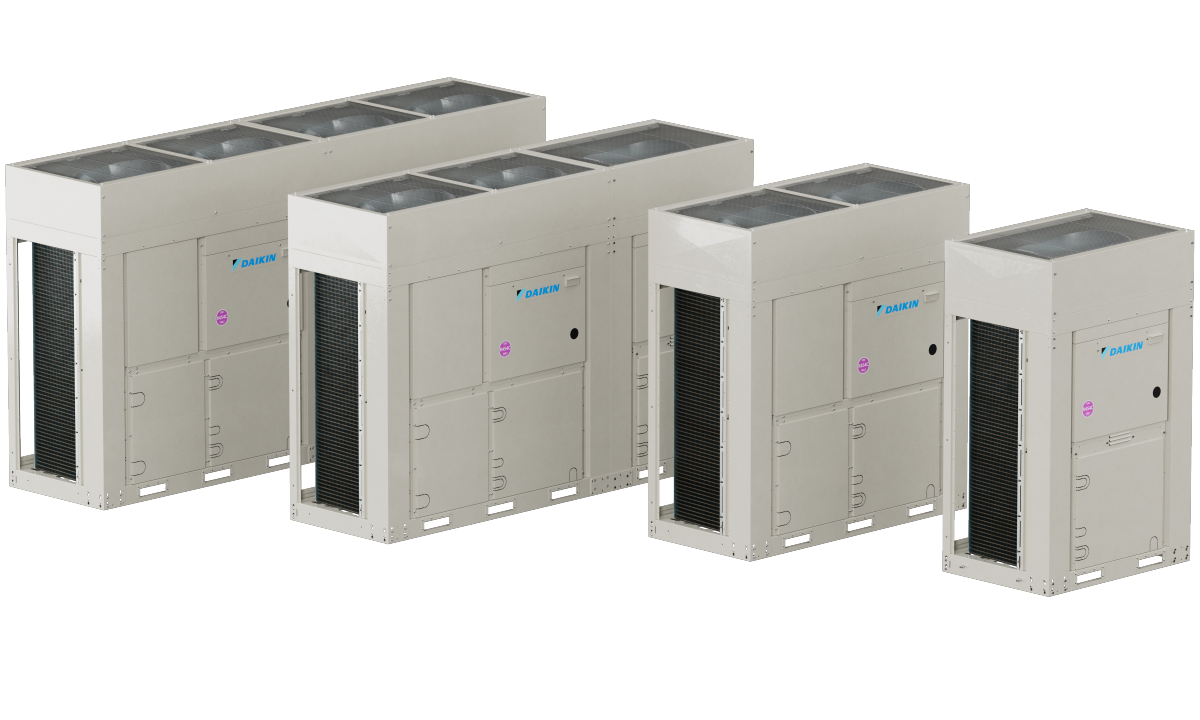