An Italian research group has fabricated a 110 cm² perovskite solar panel with an inverted configuration and a hole transport layer that uses nickel oxide instead of the commonly used poly(triarylamine) (PTAA). The proposed architecture aims to achieve high efficiency that is competitive with PTAA-based panels while improving stability.
Researchers from the University of Rome Tor Vergata in Italy have developed 15 cm x 15 cm inverted perovskite solar modules based on a hole transport layer (HTL) made of inorganic nickel oxide (NiOx).
“Our research stands out for optimizing the deposition of nickel oxide over a large area using the blade coater, a scalable technique that is fundamental to narrowing the technological gap between basic research and commercialization,” said the lead author of the paper. research, Luigi Angelo Castriotta, pv magazine. “This technique is optimized to run in standard environmental conditions with an average humidity of 25%, eliminating the need for controlled environments such as nitrogen, which are often used in traditional production methods.”
In inverted perovskite solar cells and modules, the perovskite cell material is deposited on the HTL and then coated with an electron transport layer (ETL) – the opposite of conventional device architecture. Inverted perovskite solar devices typically exhibit strong stability but have lagged behind conventional devices in terms of conversion efficiency and cell performance.
The scientists explained that inverted perovskite cells commonly use an HTL based on poly(triarylamine) (PTAA), which they said is known for its high performance in printable devices. Their choice of NiOx was due to the improved long-term stability this material offers, in addition to comparable efficiency levels to PTAA. “Unlike PTAA is NiOX is potentially cheap due to its inorganic nature, is highly photostable, chemically stable, has excellent optical transmission and has a hydrophilic nature,” they explained.
However, they also warned against the integration of NiOX HTL under ambient conditions using printable methods results in lower efficiency compared to PTAA-based devices. To solve this problem, they decided to print NiOX over the cell, without any spin coating step, via so-called doctor blades, a method generally used to form films with well-defined thicknesses.
“We have the squeegee made of nickel(II) chloride (NiCl2·6H2O) solution on indium tin oxide (ITO) substrates, ambient conditions,” the group explained. “The films were then annealed at 300 C to promote decomposition and oxidation, using atmospheric oxygen to form the NiO.X film.”
The solar panel is built with an ITO substrate, NiOX HTL, a self-assembling monolayer (SAM) made from [2-(3,6-Dimethoxy-9H-carbazol-9-yl)ethyl]phosphonic acid (MeO-2PACz), a perovskite absorber, an ETL that relies on buckminsterfullerene (C60), A bathocuproin (BCP) buffer layer and a copper (Cu) metal contact.
Image: Image: University of Rome Tor Vergata, communication material, Common License CC BY 4.0
The first four layers were fabricated via squeegee blades under ambient conditions, while the remaining layers were assembled via thermal evaporation.
“We found that introducing the SAM between nickel oxide and perovskite significantly improves the morphology and uniformity of the perovskite film, reducing defects such as pinholes and increasing the stability of the device over time,” explains Castriotta. “
Tested under standard lighting conditions, the 110 cm² perovskite panel achieved an energy conversion efficiency of 12.6%, a short-circuit current density of 19.67 mA/cm2 and a fill factor of 63.49%. The device was also able to maintain 84% of its initial efficiency after 1000 hours of thermal stress testing at 85 C in air.
“These results underline the potential of NiOX in PSCs and open new avenues for the large-scale, cost-effective production of perovskite solar panels,” the academics said. “Future research should focus on further optimizing the manufacturing process and investigating the commercial viability of these technologies.”
The new approach was presented in the study “Stable and durable perovskite solar panels by optimizing the nickel oxide deposition of the blade coating over an area of 15 cm x 15 cm”, published in communication materials.
“Our research not only addresses one of the main obstacles to the commercialization of perovskite solar cells, namely the scalability of the production process, but does so with a sustainable approach that avoids the use of toxic solvents and complex production environments,” said Castriotta. “The result is a promising technology that can accelerate the adoption of perovskite solar cells on an industrial scale, while maintaining high efficiency and long-term stability.”
This content is copyrighted and may not be reused. If you would like to collaborate with us and reuse some of our content, please contact: editors@pv-magazine.com.
Popular content
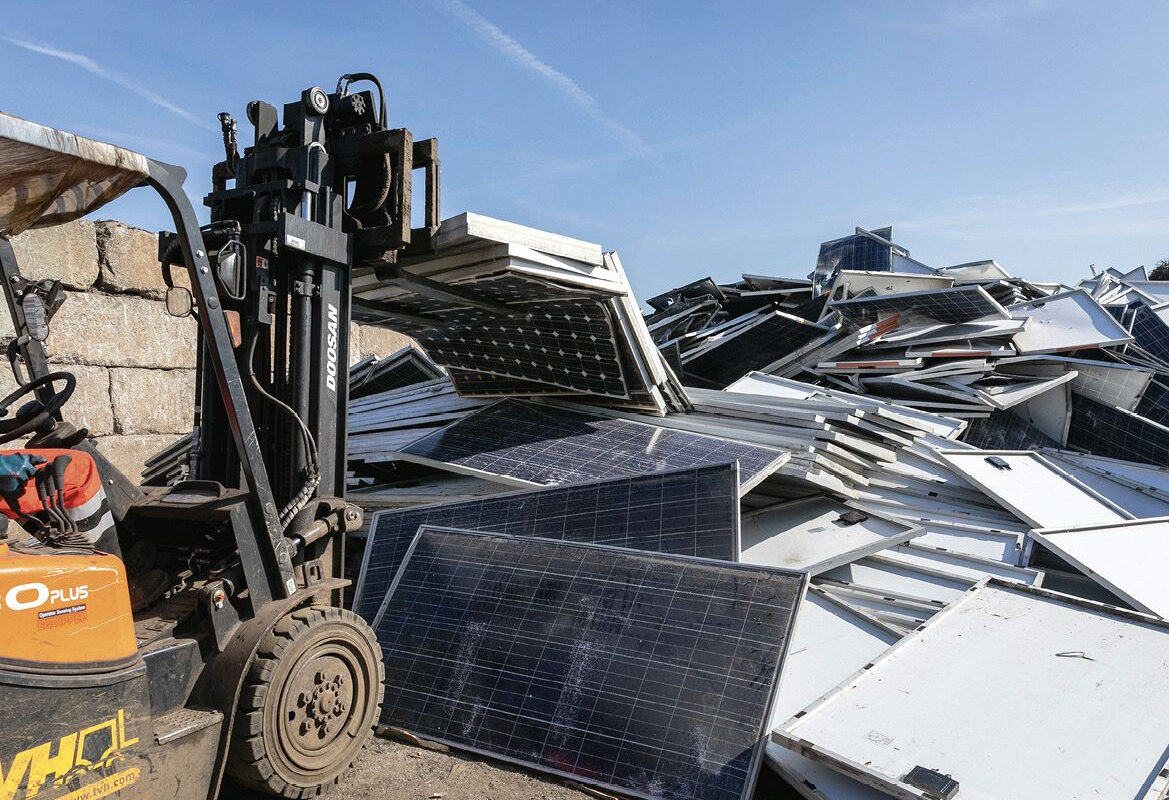