Polymer -back shoes have received little attention in recent years, in the midst of doubts about sustainability and limited transparent polymer options. Instead, modulemakers used glass on both sides, especially in the large -scale project segment. About 45% of the modules that are currently being produced still have behind, and although the trend to glass glass is set to continue, the back-let demand is said to rise.
“Predictions indicate that the global demand for polymer -rear materials will grow with an annual compound growth rate of 12% from 2021 to 2030,” said Karl Melkonyan, chief analyst for SOLAR at S&P Global. “However, the total share of all PV-back-sketch materials is expected to fall by approximately 3% per year during the same period, largely as a result of the rising trend of glass glass modules.”
A recent change to the backsheet material may have been under the radar for many. Until 2020, back shoes typically include a core cap layer laminated with polyvinyl fluoride (PVF) or polyvinylide fluoride (PvdF), but CPC products replace that option.
Three of the largest suppliers of China – Jolywood, Cybrid and First PV materials – attached to PV -Magazine That CPC products are now mainstream and amount to more than half of their backheet turnover, or more than 90% in the case of Jolywood.
The change has been fast. Speaking at the European Photovoltaic Solar Energy Conference and Exhibition (EUPVSEC) in September 2024, Gernot Oreski, division manager at Austria Polymer Competence Center Leoben (PCCL), known data that CPC-Backsheet Product Market share in 2020 to 50 % in 2020 in 2022.
That share is probably greater now, with Melkonyan explaining that “recent market trends indicate that the share of CPC back shoes has more than doubled within a year.”
Manufacturers confirm that cost reduction is the main reason for the material switch. Cheng Xudong, general manager of the new material business unit of Jolywood, explained that laminated rear magazines require extra adhesives and films, which have seen recent price increases and import restrictions. The lamination process itself also has extra costs. “Coated back shoes use fluorocarbon coatings as raw materials, which have a wide range of sourcing channels and are cost control,” said Cheng. “Coated back shoes have a simpler production process, with lower investment costs for coating equipment and less energy consumption.”
CPC benefit
Backsheet manufacturers say that, apart from cost reduction, they see other benefits for the use of coated instead of laminated products. Cheng said that the adhesives used in laminating are often a weak point, because it is known that they mitigate or designs under circumstances of high temperature or humidity. He also noted that a correctly applied and cured coating can form a dense structure on the surface of the rear, while lamining can leave holes between the two film layers, allowing possible moisture and oxygen to reach the inner effect of a module.
Cheng added that CPC screens provide further benefits in terms of flexibility, because coating formulas can be adjusted to develop back shoes with performance characteristics that match different installation environments and various basic film materials can also be tested. “By adjusting parameters such as coating thickness, hardness and color, they can adapt to different climatic conditions and installation -requirements and develop a more diverse range of back -sketch products,” he said.
The Jolywood representative also noted that CPC with environmental benefits is supplied compared to laminated back shoes, because separating and recycling a coating and basic polymer is much simpler than pulling laminated layers apart. They also offer a reduction in the use of adhesives and solvents and a thin coating consumes less material, and less toxic fluoropolymers, than a full extra layer laminated on top of a core layer.
Test
However, PV researchers and industrial observers now note a serious lack of data to support a backup of CPC performance claims. They have warned that PV manufacturers may have been reckless in accepting a new material in mass production without a complete understanding of its performance in the many different climates and environments that are installed solar energy. “The shift evokes significant reliability problems,” said Melkonyan. “The reduction in the fluorine amount and thickness endangers the protective qualities that are crucial for the durability of PV modules. While the industry insists on cost reductions, the quality of materials can unintentionally suffer, which leads to premature errors and safety problems. “
Backsheet manufacturers state that their CPC products are being tested up to and including the standards that are specified by the International Electrotechnical Commission (IEC). With Back-Scheets in particular well-documented performance problems in the field show that IEC tests are only designed to eradicate serious design errors, not to prove reliability in the long term.
Cheng said that the back shoes from Jolywood are subject to a series of tests, including accelerated ultraviolet (UV) aging, humidity and heat content, tensile strength, impact resistance, acid and alkali resistance, cooking water and water vapor transmission. He also noted that tests that expose the background scale to multiple tensions at the same time can be useful to better understand reliability in the long term. “In order to better simulate the environmental conditions that experience experience in actual applications in actual applications, his more complex stress tests required,” he said.
Combined stress tests
Cheng noted that protocols exist for combined UV, temperature and humidity tests, where modules are exposed to UV light in a climate chamber and UV/mechanical voltage, whereby material is exposed to UV light and then subject to impact, Bowing or other types of mechanical stress. Previous examples of widespread backsheet failure have led some in the industry to develop tests that are specifically designed to activate failures and determine their probability in the field, as combined accelerated stress tests created by the National Renewable Energy Laboratory of the United States and module accelerated stress tests developed. by Dupont.
So far there is little that suggests that the newest generation of CPC rear magazines is subject to such tests. PCCL’s Oreski conducted a literature study of research into PV -background shoes published between 2018 and 2023 and found that of 296 articles published during the period, only three mentioned CPC. “Analysis of the background research revealed a considerably wrong alignment between research interest and market reality,” he wrote in a paper with the assessment. “In particular the focus on materials such as PVF, PvdF and PA [polyamide] Contrasts with limited exploration of double -sided coated behind magazines. “
Oreski has also found limited data that is available at manufacturers about the specific formulations of their rear leaves and their performance under different circumstances. Of the available data, most come from smaller producers who are active outside of China. That absence has the reliability of Oreski and others involved. “I don’t try to say that coatings are bad or that these behind sheets will certainly fail,” the researcher said. “But we should have more tests and a better understanding of a material before we place it in hundreds of Gigawatt modules.”
Oreski added that although many manufacturers and third -party laboratories conduct tests to levels that go much further than specified in IEC and other qualifying standards, few long -term tests do in the long term.
Backheet failure has had disastrous consequences for PV modules in the past. Problems with the triple layer, PA-based “AAA “backs back shoes that are widely used between 2010 and 2013 are still identified, with replacement costs estimated at more than $ 2 billion alone in Germany. Since manufacturers have different coating formulases and processes, it is difficult to quantify the exact risks that the newest generation of CPC -back shoes entails. Oreski, however, noted that common coatings on the basis of polyurethane or epoxy can be susceptible to moisture damage in moist conditions, and that large temperature fluctuations and high exposure to UV light factors have been in earlier reliability problems of the back screens. Without test results, he said, “We are in a kind of limbo.”
Time and money
The costs and time required to perform combined stress tests in the long term probably explains the lack of CPC background information. This data is needed to understand the performance and any associated risks. “Without the order of stress tests, we are bad at recognizing new failure modes,” said Oreski. “We have often had great surprises in PV after a few years in the field, and we are all over research institutes and try to determine what is happening. We have to test more and with combined or successive tensions, to activate all potential failure modes. “
The few studies that have focused on reliability of the CPC -Back -Linages suggest that there can be a reason for the alarm. Researchers from the United States National Institute for Standards and Technology (NIST) subject three CPC back shoes to UV light for a maximum of 4000 hours, which simulated 45 years of exposure based on sunlight conditions in Arizona. “We characterized the chemical, optical and mechanical properties of the breakdown as a function of exposure time,” said Nist Materials Research Engineer Xiaohong Gu. “And we have observed cracks in some, but not all the samples we have analyzed. These preliminary results indicated that some transparent rear leaves also crack in the core layer of PET. “
This content is protected by copyright and may not be reused. If you want to work with us and reuse part of our content, please contact: editors@pv-magazine.com.
Popular content
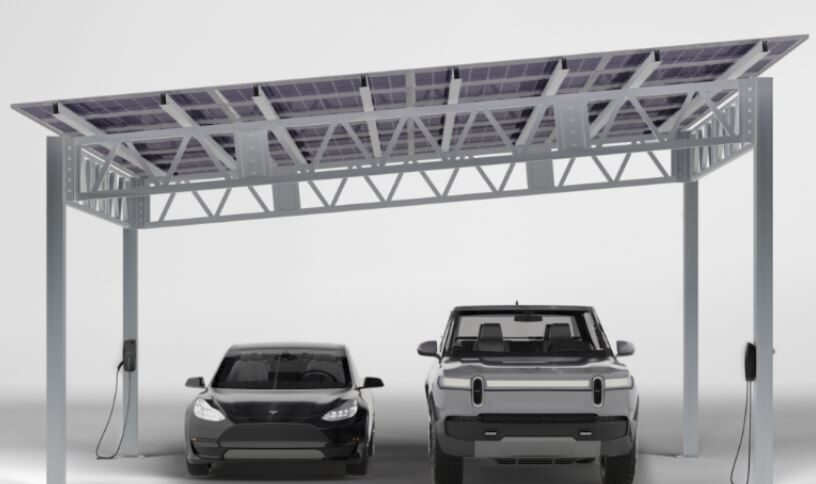