From PV Magazine 03/25
Bright Winter Sun heated a cool morning in a pleasant day in Greenwood, South Carolina, despite the threat of rain. On the last day of January 2025, around 80 attendees, including national and local representatives, and community leaders lived in a modest event in the small city to mark a great achievement for the American solar energy.
The ribbon cutting ceremony was for one Es Foundry Solar Cell Production Facility Probably the largest of the nation – for the time being. Representatives of the solar industry, Trade Press and ES Foundry customers toured through the production activities and saw crystalline silicon (C-SI) solar cells in various development phases.
“It could not come to a better time, the production of power -rising components is more important than ever,” said Elissa Pierce, an analyst for solar -supply chain at Wood Mackenzie. She said that “more than a dozen” solar module factories have been established since the IRA became law in 2022. ES Foundry is only the second C-Si Cell FAB and Woodmac expects to reach 11.3 GW of annual American cell production capacity this year.
Dun movie dominance
The American solar production is dominated by First Solar, the Cadmium Telluride (CDTE) thin film manufacturer located in Tempe, Arizona. The monolithic production process means that glass goes into one end of the production line and a finished module that comes out the other.
In the profit call of the third quarter of 2024, the first solar CEO Mark Widmar confirmed the start of production at the 3.5 GW of the company, $ 1.1 billion factory in Alabama. First solar energy is on course for 14 GW of the American module output in 2026 and 25 GW worldwide, said Widmar.
The production of thin film is housed under one roof, but C-Si-Selevingketens can be uneven. The crystalline silicon supply chain includes the production of polysilicium raw material plus solar, waffles, cells and modules separately. American cell production is still far behind the 50 GW of module capacity analyst Exawatt expected in 2025. There is no American waffle production yet.
“The companies that we have brought waffles to the US, his Suniva and Es Foundry, Hanwha brought in Waffels and Silfab brought a few waffles in January of this year,” said Alex Barrows, head of Solar in Crued Exawatt. He estimates that, from 42 GW of announced cell production plans, 10 GW could come online this year, rising to 19 GW in 2026.
Cell production
Hecapitalized Suniva began to bring 1 GW to cell production capacity online in the state of Georgia in half past 2024. The Silfab of Canada also runs a 1 GW line in South Carolina and has signed demolished agreements that start in the second quarter of 2025. Es Foundry revealed his 1 GW line in January and started the following month. Suniva raised $ 110 million in October 2023 to restart cell production, and Silfab raised $ 100 million for cell operations in November 2024.
“We have a capacity of 1 GW by August and we will intend to reach 3 GW name capacity,” said Es Foundry Chief Executive Alex Zhu, who led American activities for companies such as Suntech, Shunfeng International Clean Energy and GCL system integration. Es Foundry’s South Carolina Cell Fab is equipped for large format, “G12” (210 mm) Waffles, but currently uses smaller “M10” (182 mm) materials. “For the actual output, because we now use M10, you probably need a discount on 15% to 20% of the nameplate [capacity]”The CEO said. Es Foundry is planning to switch to the production of G12 Wafer in his second expansion phase.
Cellrative
The expansion of US solar production capacity is driven by trade barriers and domestic stimuli. For developers, this policy has made PV modules produced in their own country attractive, both in terms of security of delivery and on the basis of attractive subsidies. However, the current policy shift caused by the Trump administration has caused a peak in uncertainty. The industry has been left to think about what form these measures will take in the future.
“I think almost the entire industry is waiting to see how Trump’s government is training, what details they change about the IRA,” Zhu said.
Cell producers are currently stimulated via the Inflation Reduction Act (IRA) by a tax credit of $ 0.04/W. An additional domestic content bonus is linked to a 30% investment tax credit (ITC), plus another 10% as a certain quota of components made by the US are included in a solar project on utility scale. Both measures are important, according to Zhu, however, the ITC remains the most important measure for the American solar industry as a whole.
Zhu said that if the ITC is lost or reduced early, the impact on developers and manufacturers would be in -depth. “That would considerably change the entire investment in the industry. There are so many options on the table, it is difficult to predict. Of course we will want to keep the 45X or retain the domestic content.”
Domestic content
It is likely that under Trump very large domestic content requirements can be introduced for products made by the US to be eligible for the ITC. This can be positive for cell makers, but policy changes entail risks.
“A big problem that these celf factories have is attracting capital,” says Pol Lezcano, an American solar analyst and senior employee at Bloombergnef. He said that even before the 2024 election profit, the prospect of a second Trump -was influenced the attitude of the capital market towards solar investments. “Not only does the capital freeze, it also adds a low upstream delivery risk – because you don’t know how hard Trump will go after stream -up components with ties with China.”
Although the expansion of cell capacity is encouraging, Lezcano said that producers remain highly dependent on the input of electricity components such as waffles, ingots and polysilicon. A trade war, with potential to include producers in Southeast Asian, could have a devastating effect. The production projects of marginal solar cells seem increasingly unlikely by the day.
Serious investment
Largest financing is required to determine American cell production. PV technologist Peter Fath, the CEO of production consultancy firm RCT solutions, estimates that a “fully built-in” solar cell FAB requires the capital expenditure (Capex) of a module facility three times with the same level of automation level. When things such as the construction of a clean room and complete utility costs are included, the Capex requirements can be followed up to four or even five times higher than an equivalent moduleline.
“In the US, setting up a cell factory is really difficult. Construction companies take what they can do and the same with utilities,” Fath said. He added that obtaining certification of Underwriters Laboratories (UL) for production equipment and line can rise by a maximum of 20%in advance. This can be a fine for suppliers of Chinese equipment in particular, who may not have made that obstacle.
In the midst of policy uncertainty, the potential for export controls on Chinese PV cell equipment that connected to the United States also causes concern. At the beginning of 2024 there were reports that the Chinese government would introduce restrictions in retaliation against US commercial barriers to the import of module from China. However, industrial analysts report that import data demonstrate that checks on equipment have not been imposed, at least in the current first wave of investments in cell capacity.
River food
The purchase of other electric materials can be problematic. LEZCANO said there might not be an end to American manufacturers – with potential for new bottlenecks along the Supply Chain. “Everyone wants to get hold of non-Chinese polysilicon, and Wacker, Hemlock and OCI can charge a premium. If you try to produce waffles, you compete against a long list of companies.”
The decision to Vote the production in REC Silicon’s Moses Lake Facility Is not only a blow to non-Chinese Polysilicon shares, it may also have given a break to Hanwha Qcells. The manufacturer had ambitious cell production plans, but Lezcano said that a proposed 3.3 GW, fully integrated production facility in Georgia could be postponed as a result.
“It was quite an investment by Hanwha, the parent company – quite a big gamble. Internal [the fact that] The deal has not succeeded, can cause management delays, “said Lezcano.
Qcells seems to have fallen on schedule when setting her American cell lines. Manufacturer and project developer Canadian Solar can also let customers wait for new cells of the $ 800 million, 5 GW facility in Indiana, announced in October 2023.
Despite subsidies and supporting trade measures, the road to success in the production of crystalline silicon in the United States remains difficult to navigate. Silfab hopes the negatively doped, “n-type” cells that it produces in both the module products on the roof and to be used in aid scale, and Suniva also delivers to modulemakers from third parties. Es Foundry tries to control cell production before he is considering becoming a member of the busy Modulemarkt.
In contrast to Europe, which remains overwhelmingly dependent on Chinese import to deliver its solar projects and installers, the United States goes on the way to a ongoing milestone. The Barrows of Exawatt said that import data before February or March will probably reveal that American manufacturers who deliver more than 50% of the end market demand in the country – if only for modules at this stage.
“You will soon see from the import data that the US has shifted from a market that imports almost completely modules, something like a year ago, to a market that mainly imports cells – but still imports a few modules.”
[Editor’s note: Since this article was written, Mission Solar announced a solar cell factory in Texas anticipated to produce 1 GW by Q1 2026.]
This content is protected by copyright and may not be reused. If you want to work with us and reuse part of our content, please contact: editors@pv-magazine.com.
Popular content
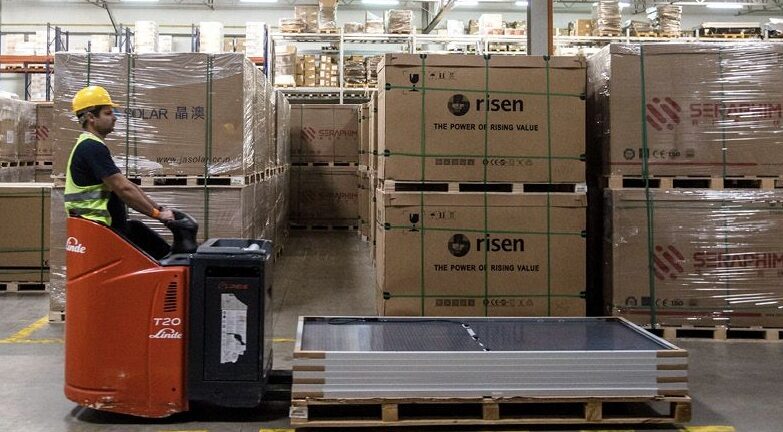