Smaller solar manufacturers have shut down production lines, but not at a pace fast enough to return profit margins to healthy territory. InfoLink’s Amy Fang considers what’s in store for PV companies in the near term.
Printed edition 24/12 from pv magazine
Economic headwinds and changing policies have slowed the global solar energy market in the second half of 2024. The discussion continues to focus on how to alleviate the oversupply of PV systems.
InfoLink has conservatively forecast solar demand of 492 GW to 568 GW in 2025, but this could be even weaker and possibly fall below the 469 GW to 533 GW expected for 2024.
Since July 2024, older production lines have been phased out and new factories have adjusted and even postponed production, but negative profit margins have occurred and the pace of profit recovery remains slow.
China’s solar industry has been trying to address oversupply. Chinese industry associations have begun actively coordinating prices and calling for self-regulation among manufacturers based on cost guidelines. Regulations that prescribe higher product quality standards are also possible. However, it will take some time for such supply-side reforms to take effect and InfoLink will monitor developments.
Supply chain
Wafer makers, the smallest segment of the solar supply chain, could produce 2.3 times more product than demand. Comparing production capacity across the supply chain with module demand shows that the gap is closing, but the pace of capacity closures is slow. The continued oversupply has caused spot prices to fall below cash costs in some parts of the supply chain, leading to a price inversion situation.
The second half of 2024 is expected to see accelerated capacity elimination and phase-out in several segments. This includes the capabilities of new entrants as well as those of Tier 2 and Tier 3 manufacturers.
Polysilicon production has been highly consolidated and manufacturers are studying similar products for fear of losing market share.
It is expected that the capacity reduction in the polysilicon segment will not be completed quickly. On the ground, some Tier 3 companies began closing in the third quarter of 2024. Tier 2 producers are struggling and new entrants are in a difficult position. Meanwhile, leading companies are also facing serious pressure on profitability and the challenge of cash flow losses across the board. These factors are expected to accelerate the outflow of larger-scale production capacity in 2025.
At the mid-range of the supply chain, production capacity growth for the wafer segment has noticeably slowed as companies seek to differentiate products by improving quality and changing product sizes. Production of positively doped p-type wafers continues to decline, with fewer manufacturers producing 182mm and 210mm wafers. Some Tier 2 and Tier 3 manufacturers may face operational crises. As existing capacity is phased out more rapidly, gross profit margins are expected to return to healthier levels in 2025 and 2026.
Cell and module
The cell production capacity clearance rate is faster than other segments, mainly due to the impact of technological advances. From 2023 to 2024, the timeline for surviving and phasing out p-type cell production capacity has become an important evaluation focus for companies. Older p-type capacity is unlikely to survive in the long term. In the third quarter of 2024, companies have started shutting down p-type capacity in China, and overseas cell capacities, especially in Southeast Asia, have also started to be phased out due to tightening US trade policies.
Decision-making in the module segment was relatively slow. This is partly because a large part of the module capacity has been installed in 2022 with a low risk of adjustments and relatively low investment costs. In the meantime, market conditions have led to a significant decline in factory utilization rates, which in turn has led to rising costs, making it difficult for manufacturers to make decisions. It is possible that manufacturers will respond by attempting to transfer second-hand equipment to factories abroad.
New entrants and Tier 2 and Tier 3 manufacturers have begun to slow capacity expansion, with some temporarily halting production. Plans for the closure of most Tier 1 manufacturers and capacity handling in Southeast Asia remain unclear. As of September 2024, an estimated 25 to 30 GW had been confirmed to be closed and approximately 150 GW was temporarily shut down or restructured.
Continued price declines will force more companies to exit the market. However, if we consider the strategies of the producers, the decision-making process on capacity release is – again – slow, as market competition makes it difficult to achieve a significant large-scale capacity reduction in the short term. This will lead to inventory problems becoming a normalized problem in the future.
As a result, factory utilization rates may not return to previous highs. Nominal production capacity across the solar supply chain has reached 1 TW, with expected utilization levels expected to be around 50% to 70%. The utilization rate of Tier 2 and Tier 3 can be 20% to 40%. Lower usage will increase the depreciation of construction and equipment costs. When usage drops to 20%, the cost increase starts to multiply. Given the long-term impact of operating below cost, this will have a greater negative impact on the wafer and cell segments. The supply/demand ratio is expected to return to around 1.7 in 2026, approaching the levels of 2021 and 2022, leading to a more balanced market situation.
About the author: Amy Fang is an InfoLink senior analyst focusing on the solar cell and module segment of the PV supply chain and working on price trend forecasts and production data.
This content is copyrighted and may not be reused. If you would like to collaborate with us and reuse some of our content, please contact: editors@pv-magazine.com.
Popular content
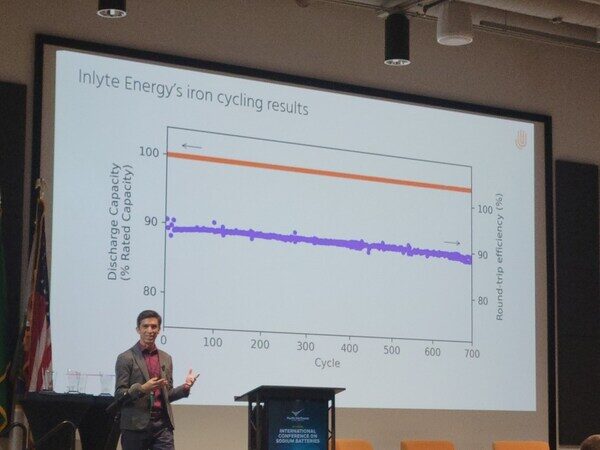